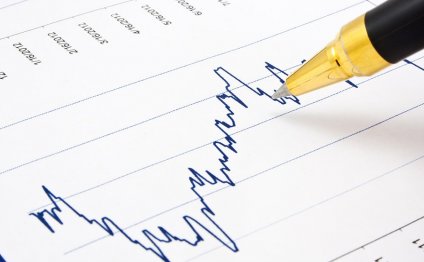
Equipment Maintenance Plans
Download Developing Equipment Maintenance Plans Whitepaper (PDF)
Executive Summary
Planned maintenance has to begin with a plan in mind. Developing preventive maintenance tasks or procedures for your plant or facility without a solid plan will result in inconsistent and unreliable procedures. Because it is important to document the development process, build-in consistency, and develop a good understanding of expected results, the Equipment Maintenance Plan is a powerful tool.
Equipment Maintenance Plans
The Equipment Maintenance Plan, or EMP as it is commonly called, is a document, in table format, that is used when developing the tasks needed to properly maintain facility, plant or process equipment. The EMP helps lead the person or persons developing the required maintenance tasks by ensuring that the development is done consistently for all equipment. Each EMP should include one or more maintenance tasks designed to ensure the continued operation and maintenance of an equipment item, process or system. Each of these tasks has the following characteristics:
- A descriptive title for each maintenance task to be performed
- A frequency assigned for performing of each task
- Assignment of a specific craft or workgroup and the number of each craft or workgroup required to perform the task
- Equipment condition required for performance of the task (i.e. running or shut down)
- Type of Work – Preventive Maintenance (PM), Predictive Maintenance (PdM), Corrective Maintenance (CM), Situational Maintenance (SIT), etc.
- Procedure number – Unique identifier for the task, or file name if linked to another document that gives the individual task instructions
- Estimated time to perform the task
- Special tools, materials and equipment required to perform the task
The EMP can also provide the following additional planning and budgeting information if set up properly in a spreadsheet format:
- Annualized hours for performing the task
- Annualized hours for shut down of the equipment during performance of the task
- Annualized hours for performance of the task by craft
Each EMP consists of the following defined sections that contain specific information (See example EMP at the end of this paper):
EMP Header
- Equipment Type – this identifies the equipment type or class to which the maintenance tasks apply, i.e. fans, centrifugal pumps, belt conveyors, etc.
- Description – identifies the specific equipment that is covered by the EMP, usually the equipment number and description, as listed in the CMMS is used here
- Location – number identifies the physical location of the equipment within the plant or facility
- Documentation – number lists what technical documentation is available and where it is stored or maintained
- Validated – this area requires a “yes” or “no” indication of whether or not the equipment nameplate data has been validated
Maintenance Task Description
- Item number – identifies each of the maintenance tasks listed on the EMP, giving each a line item number
- Maintenance task description - this area is where the very brief description of the work to be performed is entered, i.e. Clean and lubricate pump, inspect and lubricate fan, etc.
- Frequency - identifies the frequency at which the maintenance task is to be performed, i.e. 7 days, 30 days, 90 days, 180 days, 365 days, etc. Usually days are used, rather than weekly, monthly, quarterly, etc. Meter-based frequencies can also be used, i.e. 100 Hrs, 500 Hrs, etc. Situational frequencies based on inspection results can also be included
Task Support Information
- Craft - identifies the type of craft or skill required to perform the maintenance task, i.e. MECH, ELECT, CONTR, etc.
- Craftsmen required - indicates the number of crafts persons required to perform the maintenance
- Equipment condition – indicates if the equipment must be running or shut down when certain maintenance tasks are performed
- Type - the type of maintenance task is entered here, i.e. PM, PdM, CM, etc.
- Procedure/Task number – the unique procedure or task number is entered here; typically this will be the unique identifier used in a CMMS or a file name.
- Est. time (Hrs) – this is where the estimated time to complete the task is entered. This is an educated estimate based on previous experience or established estimating standards.
- Special tools/Materials/Remarks - identifies any special tools not usually carried in a craftsman’s toolbox, i.e., torque wrenches, man-lifts, ladders, etc. or a hazardous waste container, personal protective equipment, etc., and any additional remarks that apply specifically to performing the task.
Planning / Budgeting Section
- Annual (Hrs) – used to calculate the total annual hours required to perform each specific maintenance task
- Annual Scheduled Maintenance Hrs – used to total all the annual hours required to perform all the maintenance tasks listed on the EMP
- Annual Shutdown Hrs – Used to calculate the required hours of shutdown needed to perform all the maintenance tasks listed on the EMP
- Annual Operator Hrs – Used to calculate the total hours of operator time needed to perform the maintenance tasks listed on the EMP
- Annual Mechanic Hrs – Used to calculate the total hours of mechanic time needed to perform the maintenance tasks listed on the EMP
- Annual Electrician Hrs – Used to calculate the total hours of electrician time needed to perform the maintenance tasks listed on the EMP
- Annual Contractor Hrs – Used to calculate the total hours of contractor time needed to perform the maintenance tasks listed on the EMP.
You can develop an EMP for each equipment item, type of equipment or system. It is generally best to develop the EMP for each type or class of equipment and then apply the identified maintenance to all the equipment you have that is of the same type or class. When you have the same type of equipment, but in different operating environments, you may want to develop separate EMPs for each of them and apply different frequencies, man-hours and special tools/materials to each. The EMP is a very flexible document and can be used to accommodate almost any need for maintenance requirement development. Use it the way it best fits your needs and specific requirements.
When developing EMPs you are defining the tasks or procedures and all associated information needed for to properly maintain your equipment. You must first determine what equipment you want to include in the maintenance program and develop EMPs for those equipment items. Consider the criticality of your equipment before you start and develop EMPs for the most critical equipment first.
RELATED VIDEO
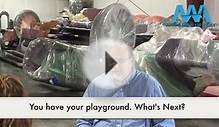
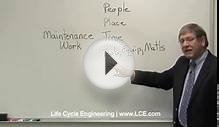
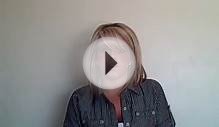
Share this Post
Related posts
Construction Testing Services
More than a century ago, PSI tested the original cables for the Brooklyn Bridge; PSI recently tested the replacement cables…
Read MoreIndustrial Maintenance Mechanic test
2) How much weight is required to balance the lever? 30lbs 25lbs 28lbs 40lbs 35lbs 3) Approximately how much force is needed…
Read More