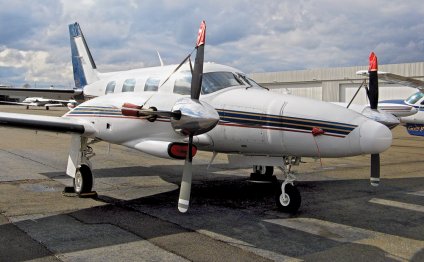
Light Plane Maintenance
Crankcase cracking is still a common problem. Do you know when to hold and when to fold?
By LPM Staff
While we will agree some cases seem more crack-prone than others, no engine is immune. Both Lycoming and Continental discuss crankcase cracking at length in service literature, understanding that it can happen and with some frequency.
Both publish guidelines for inspecting cases and offer advice on what is considered airworthy and what isn't. Some publications provide repair criteria to be used during overhaul that severely restrict where welding and re-machining of the case may be accomplished.
Generally speaking, cracks found in noncritical areas of the case are considered acceptable for service, and both manufacturers dictate where those noncritical areas are located as well as crack lengths in detailed service bulletins.
The problem is that there are precious few noncritical areas. More importantly, any crack in a crankcase, critical or not, is generally viewed as a warning flag to the unwary buyer or to the IA performing his annual duties.
Crankcases crack because aluminum castings do not like to flex and air-cooled engines equipped with opposing cylinders flex as a matter of operational functioning. The result is predictable as the case relieves normal and abnormal stresses.
Since it's virtually impossible to determine which of these stresses has produced a crack, all are viewed-or should be-with a sense of foreboding. For the IA, caution is advised-along with a recommendation for further inspection. For the clouded mind of an aviation dreamer, a lesson in case inspection is warranted.
A Case for Lycoming
Four-cylinder, wide-deck, Lycoming crankcases in the 160-horsepower and lower category are somewhat free from cracking in areas that require immediate engine removal and disassembly. They do, however, have a propensity to crack in the lower-forward portion of both left and right case halves just forward of the oil sump.
In general, cracks of this sort are long, run fore and aft, and leak copious amounts of oil. The oil is pushed through the crack by normal crankcase pressures, and though catastrophic failure is less than imminent with such occurrences, the shear volume of oil leakage could be considered a fire hazard.
Cracks also occur with regularity around the starter and alternator support bosses-not the mounting pad itself, but the thin crankcase areas securing standoffs and alternator belt adjusting arms.
Cracking of both left and right lower case-half bolt bosses is also common-usually about the fourth or fifth bolt from the front.
Lycoming engines in the 180- to 200-horsepower range are similar in construction to the lower horsepower engines and are susceptible to the same kinds of cracks. However, some of these engines, and a small percentage of the 160-horse versions, will develop what is commonly called a "smile crack."
This is a long crack that starts at the lower forward stud on the number-two cylinder, moves inboard toward the center of the case, then travels aft and upward toward the rear part of the same cylinder. This crack is small and difficult to see in its infancy, but it will leak oil as the crack progresses, until the length of the "smile" reaches "red alert" status. In some situations, the number-two cylinder has departed with the lack of deck support due to this kind of unchecked crack.
The primary place to find a Lycoming six-cylinder wide-deck crack is in the upper front corner of the number-six cylinder. This crack is common and is generally caused by case design rather than by a particularly stressful event. In addition, cracks in and around the oil filler tube located between the number-four and the number-six cylinders are common enough to be a standard inspection item.
Like the four-cylinder case, these big-bore cases also crack at the lower forward stud off the number-two cylinder deck and travel aft just above the drainback tube fittings.
Older wide-deck six-cylinder engines lacked a reinforcing rib on the lower forward outboard corners of the case adjacent to the oil sump. Cracks in these areas are usually six to eight inches long and occur with disturbing frequency. These "lightweight" cases were produced until the late 1960s, after which a beefed up version was introduced.
From 1980 on, the Lycoming wide-deck crankcases evolved into a much better casting than previously made. However, none of the wide-deck cases-even those produced today-withstood cracking like the old narrow-deck designs. In the four- and six-cylinder models, the narrow deck seldom cracked in areas that required removal and disassembly-unless the crack was preceded by the throwing of, say, a connecting rod or some other internal engine organ.
Since Textron-Lycoming is no longer providing narrow-deck engines, and given that the wide-deck version is preferable from a marketing standpoint, it may be assumed that we have once again advanced backward in technology.
Continental's War on Cracks
There is a direct correlation between horsepower output and Continental case cracking, which is why lower-horsepower engines of this make suffer little from in-service cracking. In rare cases (no pun intended), an O-200 or O-300 case will originate a crack from one of the cylinder deck studs.
In general, the crack is small and will not leak oil. These engines will, however, crack internally across reinforcing ribs at the center main journals. It isn't an external crack, nor is it one that causes much more than some main bearing fretting, but identification and repair by a crankcase overhaul facility is mandated-and only at overhaul.
The Continental 360-series crankcases are somewhat quirky in that cracking occurs in very specific areas. Problematic for these engines is cracking at the upper rear through-stud on the right case half at the number-one main journal. This will be the number-one cylinder through-bolt that secures the number-one main journal.
The turbocharged version of the 360 crankcase is also prone to cracking in the area of the right rear engine-mount attach point, primarily caused by the stress applied by the turbocharger and its mount, which also attaches to the same mount pad.
Continental has no fewer than five separate versions of its Sandcast and Permold 520 crankcases with a variety of more subtle changes between the upgraded categories.
Sandcast engines (rear-mounted alternator) and the 470 series are less prone to cracking than Permolds (front-mounted alternator) but cracking does occur in the same areas as the Permolds-it just happens less. Look for thin, tight cracks about an inch long extending down from the lower cylinder base studs around the pushrod tube bosses.
Also, check the upper case-half bolt bosses for cracks through the webbing. Continental tried to fix this cracking by beefing up the case at the case split with the introduction of the Phase III "humpback" case. The likelihood of cracking in this area is greatly reduced for new cases, but it deserves a good look anyway.
Late-style Permold crankcases incorporating the 7th stud improvement were supposed to stabilize the cylinder decks to avoid cracking at the short-and through-stud holes. These Phase IV cases are a marked improvement to your engine core, but they do little to avoid cracking.
RELATED VIDEO
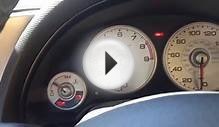
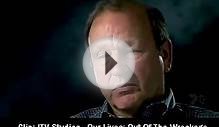
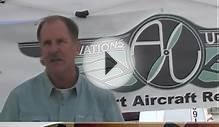
Share this Post
Related posts
Construction Testing Services
More than a century ago, PSI tested the original cables for the Brooklyn Bridge; PSI recently tested the replacement cables…
Read MoreIndustrial Maintenance Mechanic test
2) How much weight is required to balance the lever? 30lbs 25lbs 28lbs 40lbs 35lbs 3) Approximately how much force is needed…
Read More