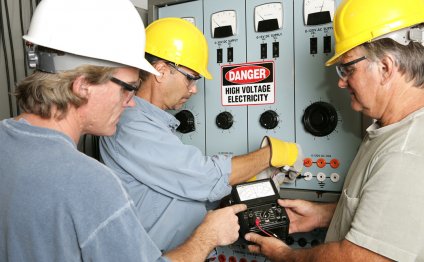
Preventive Electrical Maintenance
A well-planned preventive maintenance program is the key to dependable, long-life operation of motors and generators.
In modern plant operations, unscheduled stoppage of production or long repair shutdowns are intolerable. The high cost of the resultant downtime eats deeply into profits. Although management probably realizes the value of a good preventive maintenance (PM) program, they sometimes resist the investment in proper tools, instruments, practices, or technical assistance. Therefore, it's very important that you show how a properly planned motor/generator PM program is justified.
The first step is to show that PM pays dividends. For example, illustrate the advantages gained by employing a motor maintenance program. You can do this by collecting case histories of motor breakdowns and the cost of resultant lost production. Show how budgeted PM costs are significantly less than the cost of lost production.
Second, select the best approach. Organizing and setting up the budget for a motor PM program is usually a difficult chore. The program must be effective and, at the same time, its cost must be kept to a practical minimum. Don't underestimate the importance of this initial planning. A PM program won't work if you don't have the proper test equipment and tools, along with trained men to properly apply them. Consider which equipment you'll need and the time required to perform inspections and keep accurate records. Determine which procedures are essential and whether they should be performed by facility electricians or a service organization geared to do the job.
Finally, select the best motor-maintenance techniques. For each type of motor, controller, or related equipment, a variety of maintenance methods may be selected. Choose the best methods and determine to what extent they should be applied. For example, should you check for possible bearing trouble on a motor simply by feeling components for over temperature and listening for unusual sounds, or should you install temperature monitoring devices and make inspections using a stethoscope or an infrared scanner?
Basic guidelines to motor maintenance
Here are some valuable guidelines that you can use in your PM program.
Lubrication. Lubricate regularly according to manufacturer's instructions. On sleeve-bearing and other oil-lubricated machines, check oil reservoirs on a regular basis. In poor environments, change oil at least once a month. Never over-lubricate; excess grease or oil can get into windings and deteriorate insulation. Be sure to use only the lubricant specified for the machine in question. However, you should also check into the possibility of using modern lubricants that have excellent life and lubricating qualities.
Bearing inspection. Bearing failures are one of the most common causes of motor failures. Typical bearing problems include improper lubrication, misalignment of the motor with the load, replacement with the wrong type bearing, excessive loading, and harsh environments.
On essential motors or those that are heavily used or frequently duty cycled, you should check bearings daily using a stethoscope or infrared scanner (or camera, if appropriate). Check bearing surface temperature with a thermometer, electronic temperature sensing devices, or stick-on temperature indicating labels. Compare temperature of hot bearings with the temperatures of normally operating bearings. Check oil rings and watch for excessive end play.
Rotor/stator inspection. Check air gap between the rotor and stator with feeler gages at least annually. Measurements should be made at the top, bottom, and on both sides of the stator. Differences in readings obtained from year to year indicate bearing wear.
Belt inspection. Check belt tension; belts should have about 1 in. of play. Sheaves should be seated firmly with little or no play. Couplings should be tight, within tolerances, and should operate without excessive noise. An alignment check should be made on all motor-generator sets and on motor-load couplings when trouble is suspected.
Brush/commutator inspection. Inspect brushes and commutators of DC motors for excessive wear. Check brushes for proper type, hardness, conductivity, and fit in brush holders. Check holder spring pressure with a small scale. In most instances, pressure should be 2 to 2 1/2 lbs per sq in. of brush cross-sectional area. Call manufacturer or service company to solve recurring problems of brush chatter, excessive brush wear, and sparking, streaking, or threading of commutator.
Motor mount inspection. Check mounting bolts, steel base plates for possible warping, and concrete base for cracking or spalling.
Annually, perform vibration-analysis tests. Excessive vibration may be hard to detect by hand, but it could be enough to shorten motor life significantly. It can cause bearing failure, metal fatigue of parts, or failure of windings. The cause of vibration is usually mechanical in nature, such as excessive belt tension, defective sleeve or ball bearings, misalignment, or improper balance. The most common cause is the unbalance of a rotating member (the motor rotor, rotating load, or other drive train component). Simple testing of the motor is done by uncoupling the load or removing the belts and then running the motor. Electrical problems also can cause vibration.
Field vibration analysis can be accomplished by using a portable instrument that identifies vibrations and displays their amplitudes and frequencies.
Motor temperature control. Restricted ventilation will cause a motor to operate at a higher than desired temperature. Dirt, dust, chemicals, snow, oil, grass, weeds, etc., can clog ventilation passages of an open-frame motor. Keep motor clean and cool. In poor environments, blow out dirt with dry compressed air (no more than 50 lbs) as often as needed.
Open dripproof and totally enclosed motors are protected but must not be installed where air flow will be restricted or where excessive ambient temperatures might be encountered. In high-temperature locations, consider the use of energy-efficient motors that operate cooler than standard motors. Excessive ambient temperatures will shorten motor life.
Pull and disassemble important motors during summer shutdowns for thorough inspection, testing, cleaning, checking of bearings, couplings or accessories, or complete reconditioning.
Record keeping. Keep accurate records. Perform annual insulation-resistance (IR) and other appropriate tests. Important motors should also receive a thorough visual inspection, as well as voltage and current checks. All values should be recorded and compared each year. The trend of the readings will indicate the condition of the motor and offer a guide to its reliability.
RELATED VIDEO
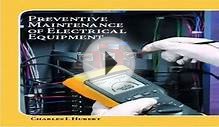

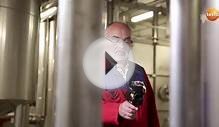
Share this Post
Related posts
Construction Testing Services
More than a century ago, PSI tested the original cables for the Brooklyn Bridge; PSI recently tested the replacement cables…
Read MoreIndustrial Maintenance Mechanic test
2) How much weight is required to balance the lever? 30lbs 25lbs 28lbs 40lbs 35lbs 3) Approximately how much force is needed…
Read More