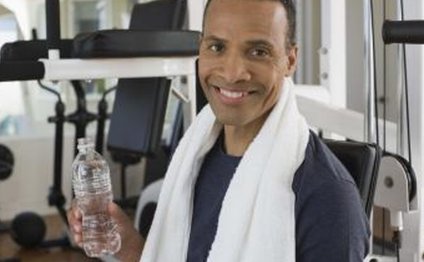
Preventive Maintenance Program Sample
By Christer Idhammar
Most Preventive Maintenance (PM) programs were set up many years ago. Each department in a plant set up their own program in isolation from each other. As an example, a plant set up a PM program covering mechanical equipment, then another program was set up for electrical equipment and another to cover automation and control system. A lubricant vendor then added lubrication routes and on top of this other PM activities such as Vibration Analysis and Operator Inspections was added in addition to all other PM tasks.
It is not uncommon to also find that many old Fixed Time Maintenance (FTM) tasks, such as programmed overhauls and replacements, are still being done on an annual basis because that is what the plant always have done, and nobody has challenged the validity of these tasks. These tasks are often driven by the availability of time and maintenance people instead of the true validity of the task. In some industries, for example food processing, there might be a seasonal period when crops are not being harvested and processed. Maintenance people are then more available and some equipment are idling, so to keep people busy some equipment are overhauled and some components are replaced. The decisions to do these tasks are often based on believes rather than facts. This presents a good opportunity to ask if the life expectancy of components in question are predictable or known, and if there is a method available to do inspections while equipment is operating. If the condition of a component can be measured while a production line is operating, then the condition of the component will determine what corrective action we can take to avoid a break down. If this is done we have chosen to do Condition Based Maintenance (CBM).
As an alternative to the above mentioned PM activities you can also chose to Operate to Break Down (OTB).
Best alternative is to Design Out Maintenance (DOM) or even better Design For Reliability and Maintainability before the equipment is manufactured. In this article I am not going to cover these alternatives, I gave some examples of this in the March/April issue of this magazine.
In 1968 I learnt about failure distribution in time and failure development periods, you might want to call this Reliability Centered Maintenance (RCM) methodology. In my opinion it is good common sense and it is the most useful part of RCM along with knowing the criticality of a component. To enable you to analyze existing PM tasks and optimize your total PM program you need to understand this concept.
Picture 1. Failures can be categorized as failure modes that develop over a period of time as visualized in the left graph. These failures have a Failure Developing Period (FDP). You can say there is a time difference between the point of failure until the break down occurs. A break down is when the intended function of a component ceases.
A completely reactive maintenance organization will act upon break downs. A better organization will find the failures before they develop into break downs. They will use the warning time they have gained by finding failures early to plan and then schedule a corrective action, and execute this action before the break down occurs. By doing so, you have started to optimize the life of a component. If you can estimate how long the FDP is you can use this information as a guide to decide the frequency of inspection. The frequency of inspection should be no less than FDP divided by two.
Best organizations are spending considerable time to not only find failures and plan and schedule their corrections, but also to find the source of the failures and then design out those failures. Your organization has then evolved to a thinking and learning maintenance organization.
If a failure develops over a very short period of time, which is typical for failure modes of electronic components, then there is no, or very short, time to discover a deteriorating condition. See the right graph. Condition monitoring is therefore not an option. In this case you can ask if the failure mode has a random or regular distribution in time. If the failure mode is random, and the FDP is very short, then it is a waste of time to do inspections of the component. You can inspect for example that the cabinet for electronic components is sealed and kept cool and clean and you should prepare a corrective action for when the failure will occur.
If the failure mode has a regular, or predictable, distribution in time, then you can consider Fixed Time Maintenance, such as overhauls or replacements on a regular basis. I propose that you analyze all your FTM activities and question if they can not be moved to CBM and if their frequencies are right. My experience is that not more than 5 - 10% of all failure modes have a regular distribution in time.
RELATED VIDEO
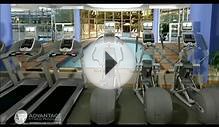
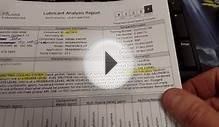
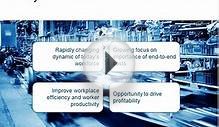
Share this Post
Related posts
Preventive Maintenance training
By Torbjörn Idhammar Classroom reliability training followed by practical experience could end money being wasted on maintenance…
Read MorePassive Preventive Maintenance
Do you know how much impact downtime costs? According to Dunn & Bradstreet, 59% of Fortune 500 companies experience…
Read More