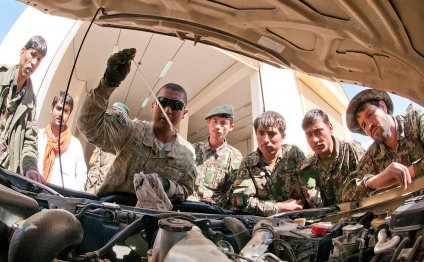
Preventive Maintenance training
By Torbjörn Idhammar
Classroom reliability training followed by practical experience could end money being wasted on maintenance courses and seminars that workers quickly forget.
Companies can spend thousands of dollars on maintenance training, but often, very little of the knowledge gained on maintenance and reliability training courses is ever used in the plant. In fact it is common for trainees to forget some of the lessons learnt, just weeks after the event. One way to help resolve this phenomenon could be to give classroom maintenance training in conjunction with practical experience.
It may be a good idea to economically justify all training seminars that are given in a plant. There is not much point in holding a reliability training seminar if it isn't for eventual economical gain. The reliability training must have a purpose that should be decided before the training starts and should never be performed unless there is a plan to implement the lessons learnt. Once the training is finished, mill management should check that the implementation plan is being followed.
Maintenance matters
Management should also communicate to trainees that:
- results are expected from the maintenance training;
- support for implementation of the reliability course will be provided;
- there will be a follow-up on the results.
Training in the maintenance department of a plant often focuses on reliability of equipment and the lowering of maintenance cost.
A good example is alignment training. Alignment is usually carried out by mechanics when installing a new pump, motor or gearbox, for example.
Conventional training on alignment would usually focus on how to use a laser alignment tool. This approach is fair enough, as most mechanics need to know how to use such equipment. But a better approach could be to include an implementation and/or an improvement plan. An alignment plant standard could be reinforced and a few pieces of equipment could be checked in the plant, so that the class knows how well-aligned their mill equipment already is. Some equipment could be realigned in the mill, so that before and after readings can be taken. An improvement plan with a goal to improve alignment could be drawn up during the training.
Many training seminars teach the theory of what to do and, at best, give some hands-on examples in the classroom. Admittedly, some plants do very well by training a few key people who then are able to transform what they have learned into an implementation process. However, most plants will put a number of people through a training class, only for the training never to be heard of again. If the lessons can be implemented in the trainees' mill during the training session, practical problems such as safety, finding the right tools, getting time from machine operators, informing supervisors and finding spare parts will become a part of the training.
Jump start
Maintenance consultant company in the USA, IDCON, has structured a training class called the Reliability Jump Start program, based on the above principles. Its program evolved from a training seminar it gave to a plant in China. The Chinese mill wanted the company to teach the concepts and then go out into the mill and demonstrate what it had talked about.
RELATED VIDEO
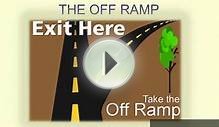
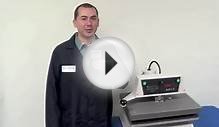
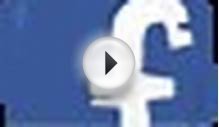
Share this Post
Related posts
Passive Preventive Maintenance
Do you know how much impact downtime costs? According to Dunn & Bradstreet, 59% of Fortune 500 companies experience…
Read MoreFacilities Preventive Maintenance
The Preventive Maintenance team of Physical Facilities perform their periodic, scheduled maintenance on building equipment…
Read More